High-pressure liquid ammonia pump export leakage and maintenance
High-pressure liquid ammonia pump P101A/B is the key equipment in the urea plant is in the 1980s, the company introduced from American SUNDSTRAND HMP - 5112 type high speed centrifugal pump, the working condition for an open a ready for export, design, high pressure 27MPa axial speed for 20445R/min, Its export check valves for single swing check valves pressure from seal structure and basic parameters, such as shown in table 1, main effect is in P101A/B fall when the pump automatically closes to prevent backflow medium to high pump impeller, protect the P101 pump. After more than ten years of operation, two valve leakage, and serious P101A pump export check valve leakage, these two fault if not timely solve will seriously affect the safety in production of urea plant, analyses the overhaul, pump export check valve leakage, simultaneously with the valve for the following example is introduced.
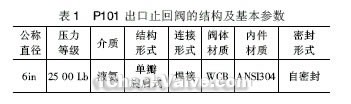
Maintenance problems when the valve
(1) the valve for heart valve in the work of the state, wear heart when grinding, cause heart valve elliptical sinking, as shown in figure 1 shows the seat sealing, frequent open, thus causing serious damage under severe leakage, as shown in figure 2.
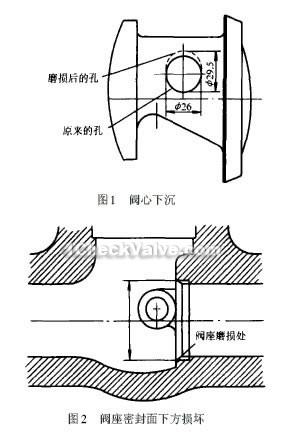
(2) the valve for manufacturing defects and medium corrosion, outside the body sealing parts, appeared in liquid ammonia leakage, as shown in figure 3 below.
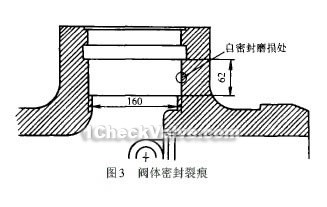
Overhaul scheme
Because of this valve is welded valve, maintenance time limit, can repair. Off-line The method to use field repair. Repair for leakage and leakage from two aspects:
Leakage repair plan
(1) with small electronic grinder manual polishing the body sealing surface colouring crack, at the same time, until all crack defects detection.
(2) choose A402 electrode (chromium and nickel and stainless steel electrode welding method, using the body heat sealing surface polishing repair.
(3) using small electronic grinder manual polishing welding, make its height and body surface basic leveled.
(4) making inner ring type grind, as shown in figure 4.
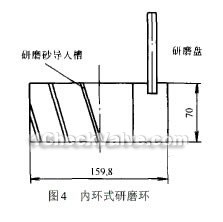
(5) in the production of sealing ring manual polishing and grinding 160.7 mm diameter: after.
(6) according to the inner after grinding deserve to be sealing, as shown in figure 5.
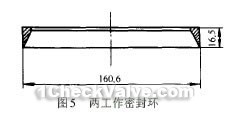
Leakage repair plan
(1) using portable grinder grinding seat sealing (see chart 2). Ensure the carbide existing in the circumstance for circular.
(2) on a lathe with four card original heart valve positioning found when wear, meanwhile, center, reaming, as shown in figure 6.
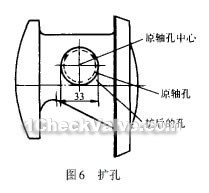
(3) car made two rings (1Gr18Ni9Ti) in reaming. In the center of that under the condition of invariable, can wear and reasonable, and welding fixed, as shown in figure 7
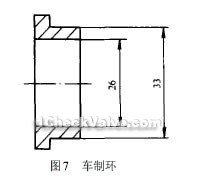
(4) of 1Gr13 wear (car).
(5) carbide D547 molybdenum electrode head, according to repair valve seat hole after grinding head matchs repair valve seal.
(6) after the match with test and ensure its sealing turns test.